製造業DX
現場目線のソリューションで
「見える化」の先の変革を実現
About us製造現場をルーツとする
DXアドバイザー
私たちは、現場課題を起点とした最適なソリューションを提案するDXアドバイザーです。
そもそも私たち自身が、自社工場でのDXに挑戦してきた経験者であり、
DXにおける試行錯誤の大変さと重要性をどこよりも熟知していると自負しております。
できる限り製造現場に寄り添い、真摯に課題を解決していくことをモットーに、
お客様に最適なソリューションを粘り強く実現してまいります。
こんなコトで
お困りではありませんか?
- 生産計画の立案が
属人的になっており、
作業が滞ってしまう - 実績や記録など
現場で紙に記入した後、PCへ転記しており
二度手間となっている - 設備の保全記録や修理履歴が
紙で管理されており、
履歴を確認するのが大変 - 入力基準が
担当者によってバラバラ。
正しい原価計算ができない - データの集計に
時間がかかり、
分析まで手が回らない - 工程の進捗状況を確認するためには
その都度現場まで行かないと
わからない
TSUBAKI’S WAY
生産性を向上させる、
データ連携DXソリューション
自社事例をベースにお客様の現場に合わせた、監視・分析機能をワンストップで提供。
現場課題を起点としたトータルソリューションにより、
生産性向上や安心・安全な環境整備を行い、
スマートファクトリー化による強い工場づくりを目指します。
POINT 1現場の実態をデータ化
様々なデータ取得手段を駆使して、
設備の情報だけでなく、人作業にかかっている時間も
データ化できます。
POINT 2全体最適をご提案
トータルソリューションとして提供することで、
部分最適ではなく全体最適による
生産性向上をサポートします。
一つひとつの対応がハートフル!
満足いただける成果が出るまで、データ分析や仮説検証を繰り返し行います。
成果を上げた後も、さらなる改善に向けてともに走り続けます。
導入までの流れ
ヒアリングで得た仮説に対して、
小規模検証を行い効果の確認を行うことも可能です。
-
ステップ1
お客様の
現場課題について、
ヒアリングシートを
用いてご確認 -
ステップ2
当社から
課題解決の対策
(DXソリューション)をご提案 -
ステップ3
お客様の現場で
当社提案の
小規模検証※ ※小規模検証の内容に応じて、
実費費用を頂戴する場合がございます。 -
ステップ4
効果確認、
お見積もり
(見積仕様書取り交わし) -
ステップ5
運用開始
DXソリューションの
現場導入 -
ステップ6
運用効果の
確認
In-house Cases椿本チエインの現場から生まれた
ソリューション事例
Case01
『多台持ち』による
設備停止時間が長く、
生産効率が上がらない
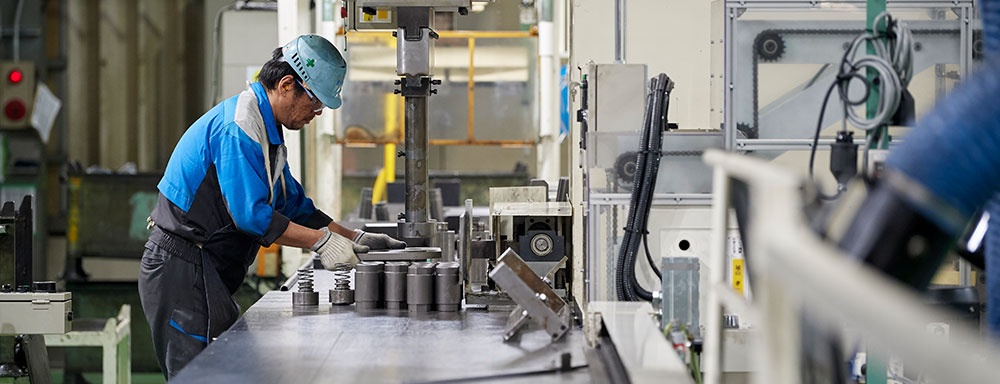
課題
設備が停止していることがわからず、「放置」されていた。
・生産の終了予定時刻がわからないため、多台持ちの運用/連携ができていない ・情報をタイムリーに共有できない ・サイクルタイムが設備や品種ごとに異なるため、個別に計算しないと正確な生産時間が把握できない
ソリューション
設備付属のPLC(Programmable Logic Controller )から
必要なデータを収集し、「見える化」画面を構築します。
設備停止までの「残り時間」とその「時刻」を生産数から自動で計算できます。
また、予定の生産数に達したため設備が停止するのか、
材料切れかなど設備停止の「理由」も明らかにします。
効果
生産効率が向上
「見える化」画面で情報を共有することで、作業の優先順位や対応者を計画的に設計できるようになりました。また、「材料切れ」「工具交換」など、停止理由もわかるのでスムーズな対応が可能になりました。
次に設備が停止する時刻が明確化
設備停止までの「残り時間」が明確になることで作業者が停止時刻に合わせた動きをするようになりました。設備が稼働していない時間を減らすことで生産性が向上しました。
Case02
生産計画自動化のために
工程標準時間のマスタを整備したい
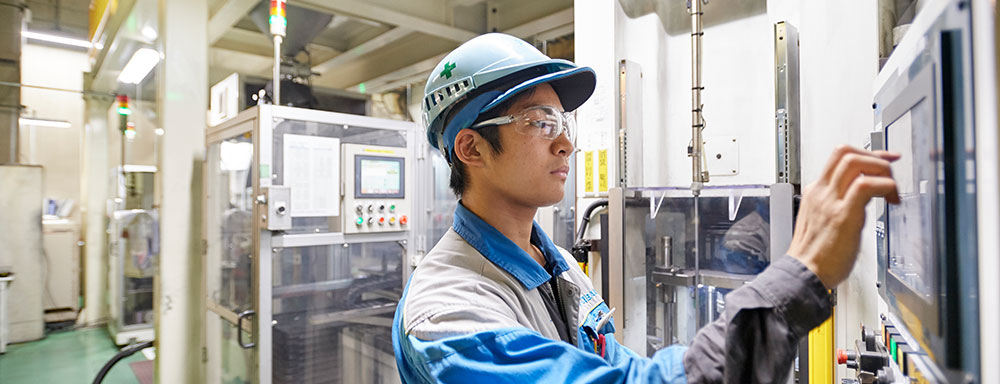
課題
「段取り時間」は、人の動きが多いため定量的な計測が困難。
・ストップウォッチでの手計測は可能だが、多くの工程に対応するためには多くの時間が必要となる。
・マスタを維持するためにも多くの工数が必要となるため管理が大変。
ソリューション
現場作業を撮影した動画の自動分析や
ビーコンなどによる作業者の位置測位によって
段取り時間を定量化していきます。
効果
段取り時間の定量化
センシングによって段取り時間を測定し、標準時間を設定することで、マスタを整備することができました。
作業のバラツキの要因分析
作業者ごとの段取り時間を収集することで、作業者によるバラツキを明らかにし、バラツキの要因を分析することができるようになりました。
Case03
「データの集計」に時間がかかり
収集データの分析や改善活動に
時間が取れない
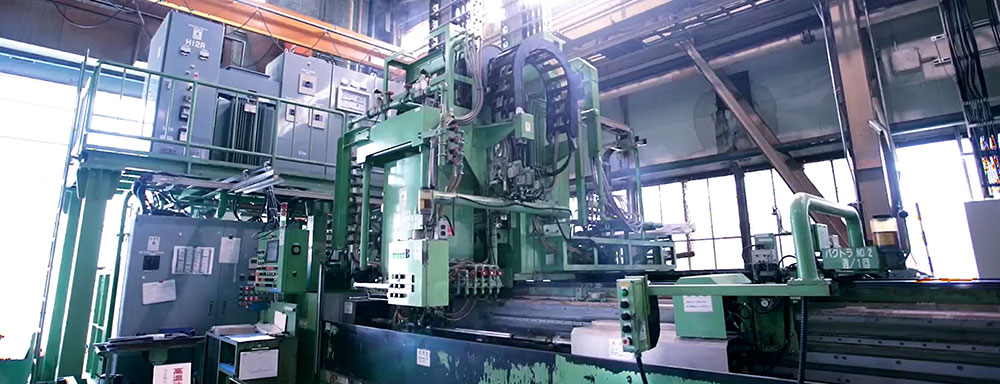
課題
エネルギー(電力やガスなど)に関するデータの集計で手一杯で
改善活動に時間が割けない。
・各設備のデータを集めるだけで時間がかかる。 ・毎月のデータの集計が完了しないと分析することができない。
ソリューション
様々なデータの集計を容易にする「集計ツール」と
改善ポイントを見つけ出すための「分析ツール」を用意し、
集計から課題発見までをスムーズに行えるようにします。
効果
「集計ツール」を活用
データの集計にかかっていた時間を改善のための分析に使用することができるようになりました。
毎月の集計を待つことなく日次データを確認できるようになりました。
「分析ツール」を活用
統計的手法をツール化することで、効率的に分析を行うことができ、問題を起こしている要因にたどり着くまでの時間が短くなりました。
に関するお問い合わせはこちらから
お手軽に始められるIoT対応商品はこちら
IoT対応遠隔監視プラットフォーム
MitaMon®
-
工場やビル内での
エネルギーを見える化する
モニタリングシステムです。
持続可能な社会の実現に向けて
つばきグループは、「動かす」分野において社会の期待を超える価値を提供し、
社会から必要とされ続ける企業となることを目指します